Sector
AI & iOT in Mining
Project Time
7 Months
My Role
UI/ UX
Designing for AI driven predictive maintenance to maximise safety and prevent injury and death
In a team of 3, I worked closely with the Gas Analytics Team in the development of their new Asset Management Portal (AMP). This portal would support the business's latest onsite line of 5G connected methane sensors to facilitate better safety KPIs, more efficient protocols and improved communications with service technicians around predictive maintenance.
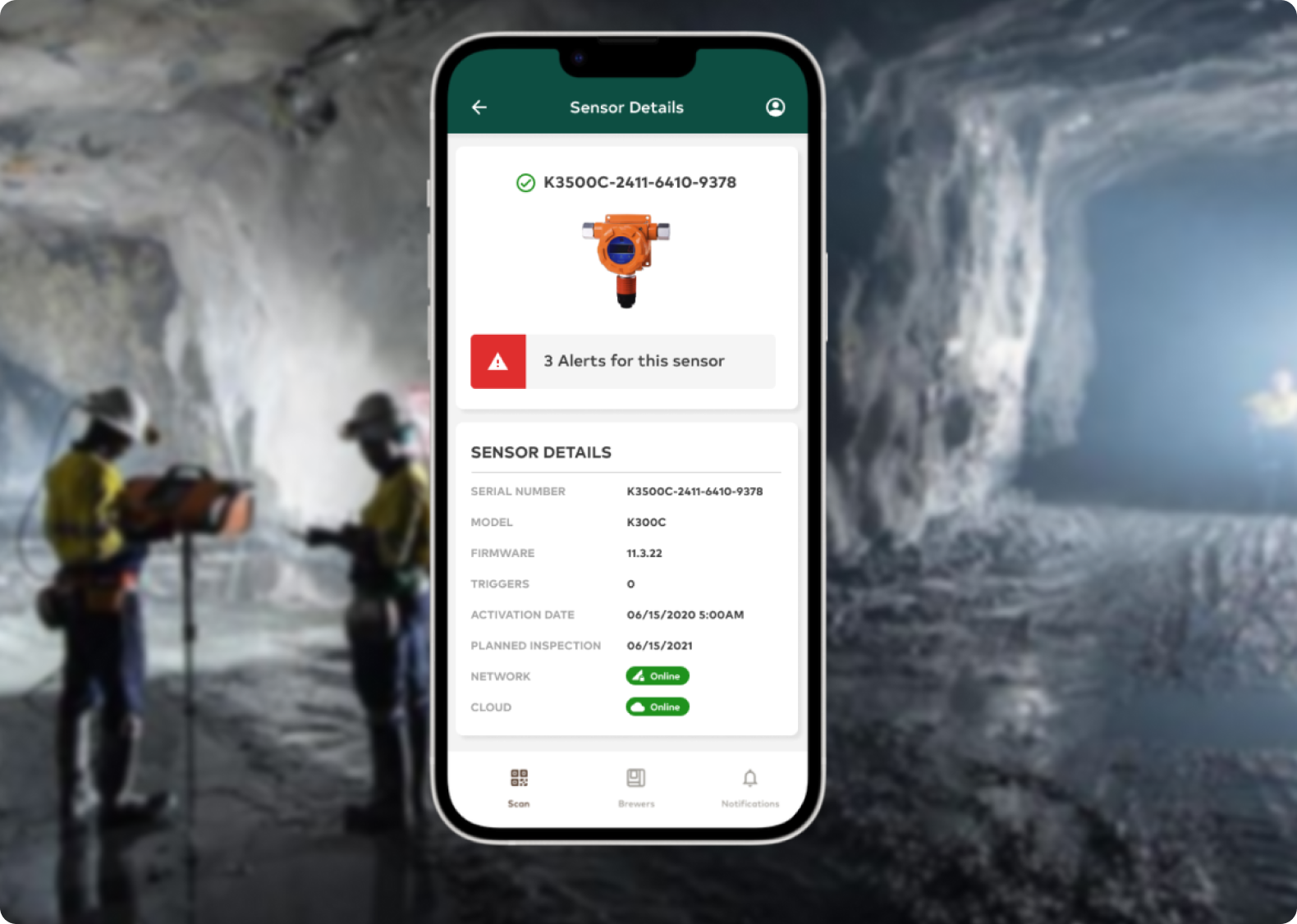
The Gas Analytics Team and their distribution partners deploy and maintain millions of sensors internationally. The processes of managing this are largely manual and are hindering site safety KPIs.
With the introduction of their first 5G sensors, the company will have the opportunity to be more proactive and less reactive with how they service their customers. My role was to work with field service teams to design the experience that helped field technicians install, maintain, and service their clients proactively with the use of ML predictive maintenance technologies.
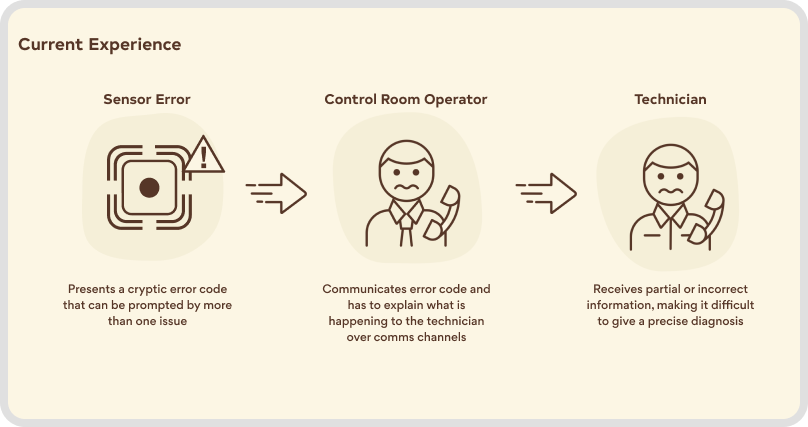
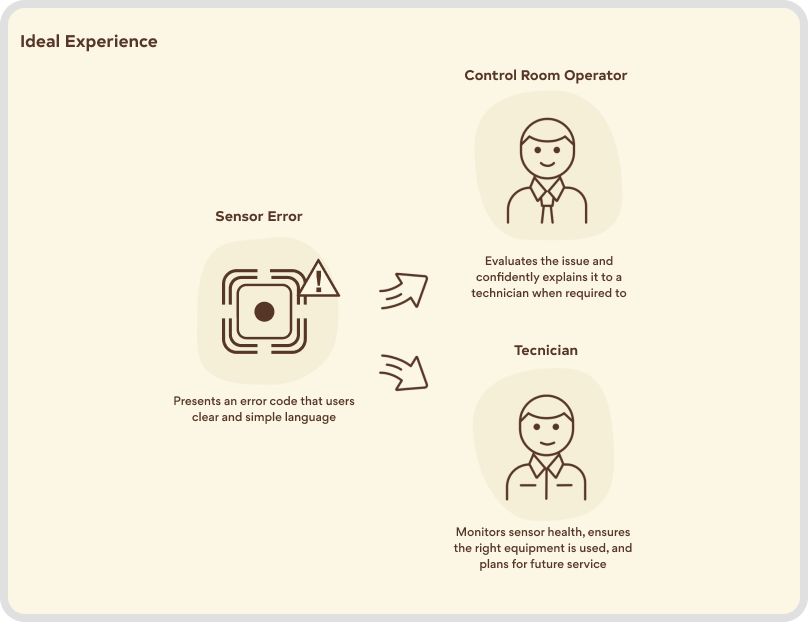
Key Pain Points Responding to Partial or Incorrect Information
Technicians need easy access to detailed information about a single sensor and the ability to troubleshoot with level 1 users over comms channels. By eliminating the need for physically being there to inspect sensors, save trips, and improving the functionality of the predictive maintenance features of the system, overall efficiency is increased.
Technicians Work Better as a Team
Technicians want to view the service history of a sensor and then use that data to use as parameters in predictive maintenance processes and discuss updates with their team.
Data Helps Diagnose
The data on the type of methane detected by a sensor and the accuracy of its reading impacted the efficacy of troubleshooting issues.
Shift from Reactive to Proactive
Technicians struggled to monitor the health of a specific sensor in different locations across various mine sites. This made it unsafe because it then required them to physically inspect sensors most of the time, it made it difficult for them to organise their backlog, including the training of staff and keeping tabs on the parts needed in maintenance updates.
Understanding the Scope
Flow DiagramsTo understand what screens and functionality was needed at the time, I mapped out flow diagrams and vetted them with the onsite and engineering teams.
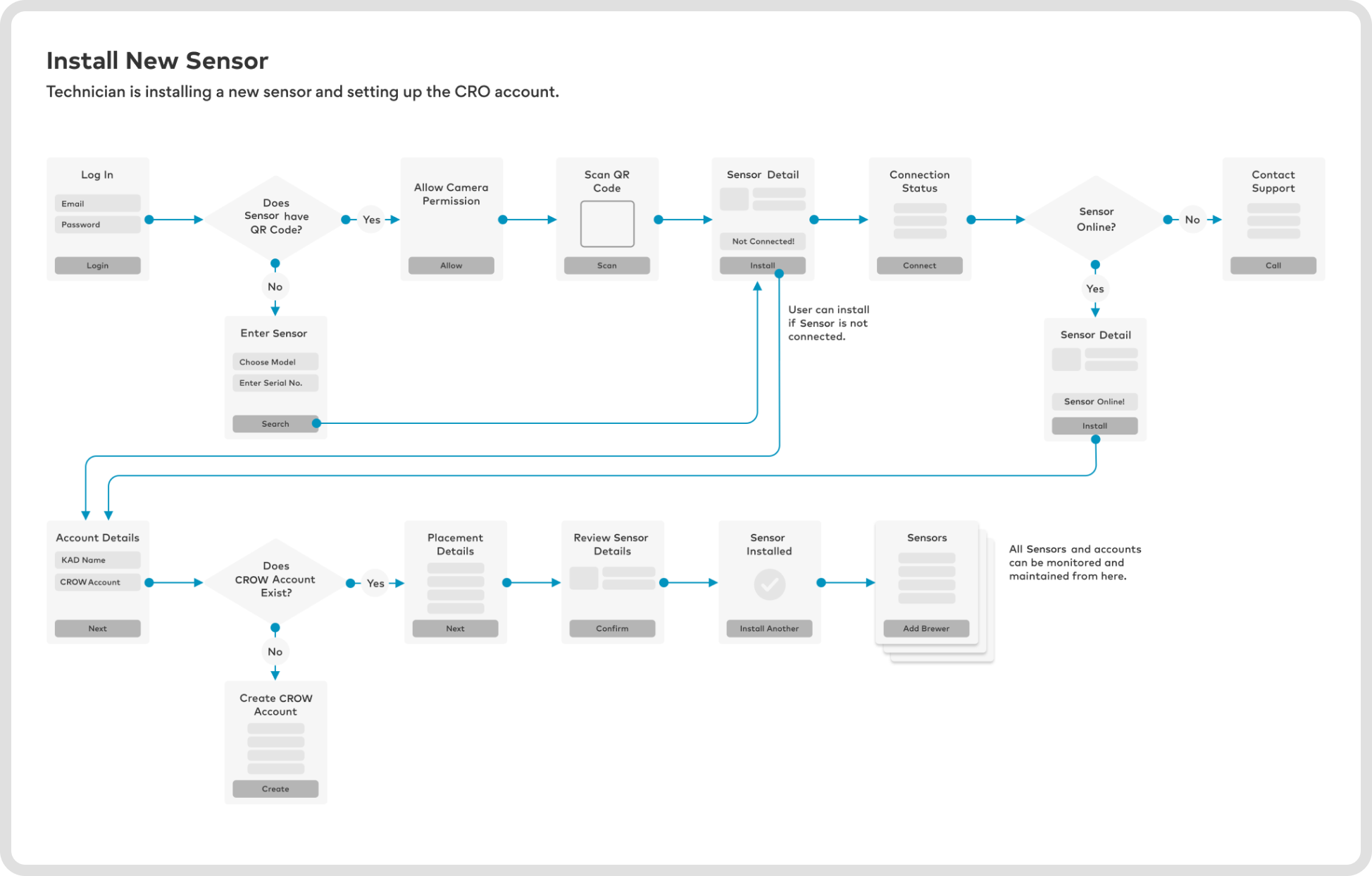
Design System
At this point, I was a regular contributor to the the company's established design system and leveraged the component library to quickly lay out the core screens. I also added mobile friendly elements.
The sites we worked with were iOS based and so focused on iOS design as the priority. At the same time, the company considered using Huawei as a preferred supplier and so I made a point of designing platform agnostic flows so that the designs would equally facilitate Android at future releases if that transition went ahead with the company.
View Errors & Input Service Reports
Technicians could collect data by scanning a QR code found on every sensor or input serial codes manually to easily view key product and account details, error codes, service history, and finally, submit service reports.
Adding Service ReportsTechnicians could track past service details and input new information.
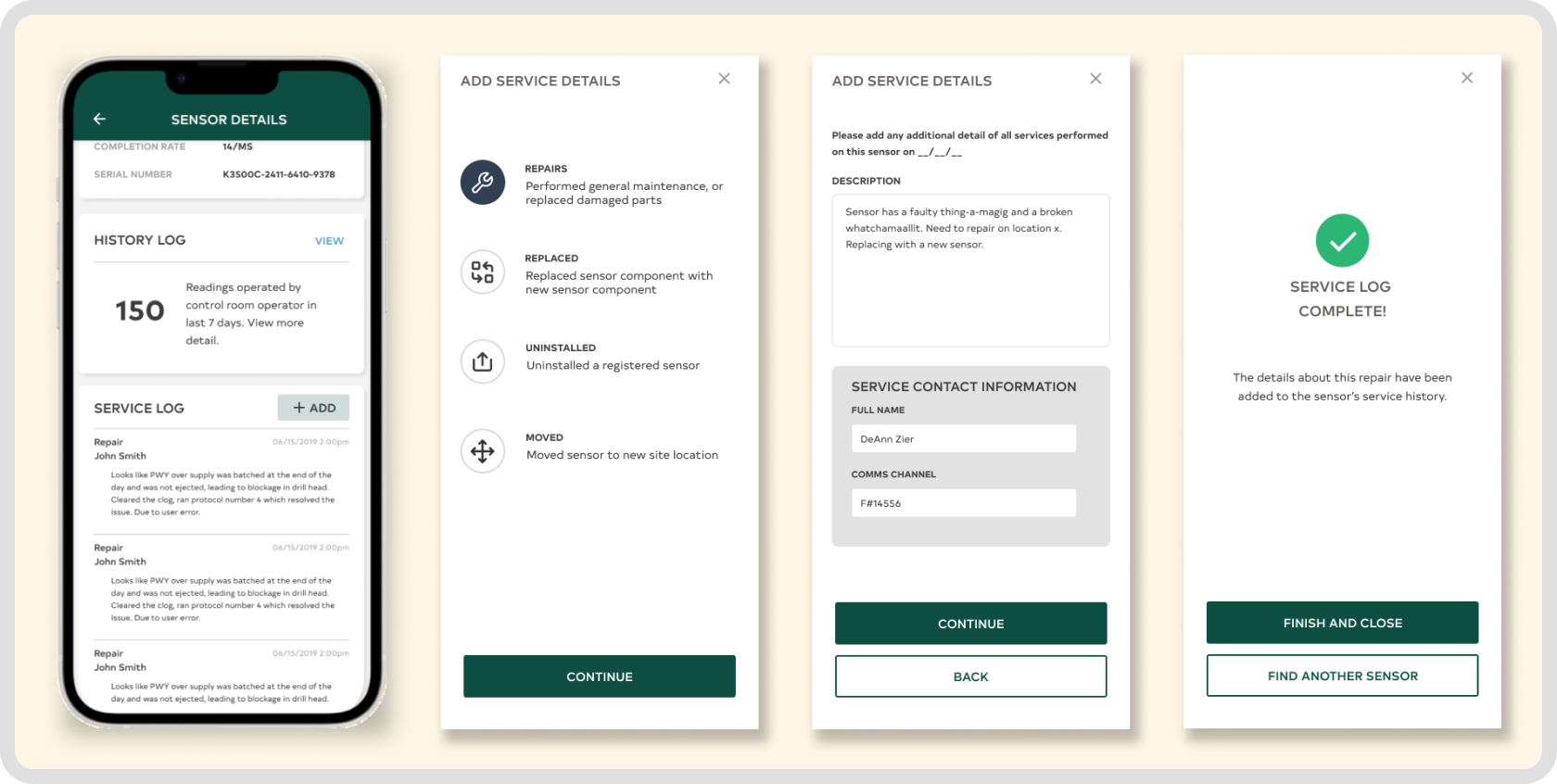
Sensor InstallationTechnicians could now easily install new sensors and add and oversee critical account data during the installation process.
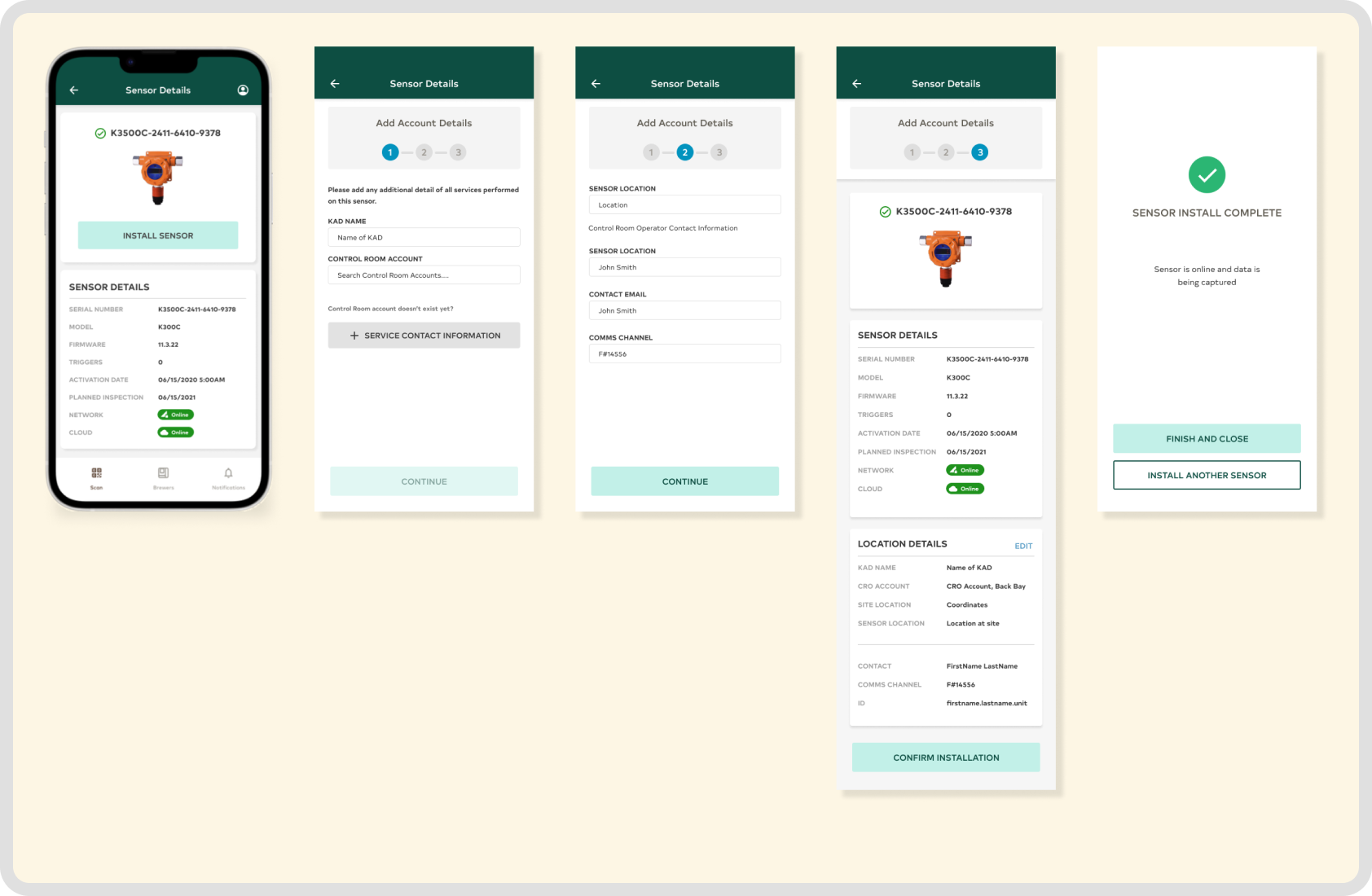
Results
Improved Safety
Because control room operators and site managers could now precisely communicate issues when sensors experienced issues, technicians no longer needed to physically travel to inspect errors with sensors, thereby minimising safety risks, travel time and optimising their routes across their teams.
Easy Data Collection
An intuitive mobile experience provided an easy way to input data that would automatically populate The Gas Analytics Teams AMP database. This gave users a safer, more effective way of doing the tasks most critical to the operation.
Better Organisation
This design improved how technicians and control room operators organised their processes around maintenance of sensors to improve safety, predictive maintenance trust and efficiency. It also helped to train their staff, and track necessary stock parts.